Project Background
The BMW manufacturing plant in Greer, South Carolina, USA is BMW’s first complete manufacturing facility outside Germany and the group’s only assembly facility in the United States. Built in 1993, the plant covers 1,150 acres and employs more than 11,000 people locally.
Currently, the plant produces approximately 1,500 vehicles per day. The plant is currently BMW’s major global production site for the X3, X4, X5, X6, and X7 crossover SUVs, where it serves the biggest market – U.S. Meanwhile other BMW models sold in the U.S. market are imported.
Project Description
BMW Manufacturing’s Landfill Gas Project was implemented in 2003 in conjunction with partners Ameresco and Waste Management. Infrastructure was installed at the Palmetto Landfill to collect, clean, and compress the methane gas; the gas is then transported through a 9.5-mile pipeline to the BMW plant. The methane gas coming from the landfill is used as the fuel source of two turbines to cogenerate more efficiently electrical power, heating, and cooling.
Project Value
Assuming that the system is running for 6,000 hours minimum, and with 0.79 of COP, we get an energy consumption of 76,64,580 kWh/year, which would be equivalent to 3316 metric tons of Co2 equivalent being emitted from the chiller. 7,670 barrels of oil consumed 3,714,429 pounds of coal burned per year.
* Results are based on US EPA CHP Energy and Emissions Savings Calculator, which may vary from the actual operation data.
Project Highlight
The project is a replacement project, which plans to replace two Trane hot water chillers.
It is the first one and the second one will be purchased in the next few years. BROAD absorption chiller won the project by virtue of its excellent performance:
- More COP as compared to others
- The lifetime of our chiller is 40 years
- Excellent service support
- Outstanding after-sales service, and a good relationship with local dealer
Many leading architects, engineers, developers, and property owners are building on steam for cooling because of the efficiency, flexibility and reliability of
steam absorption chillers, especially for buildings with existing steam-powered heating. Using steam as a heat source for cooling during the summer can help reduce electric-peak demand, therefore helping to reduce overall operating costs.
Benefits of Steam Absorption Cooling:
● Bring steam system reliability into the cooling solution;
● Avoid electric demand charges at peak rates;
● Alleviates electric capacity at peak periods for alternate use;
● Lower risk of interrupted electric service from system strain in peak periods (within buildings and within regions);
● Steam chiller provides economical “on demand” supply of chilled water as opposed to storage systems;
● Use water as refrigerant, effectively reduce ozone pollution in summer;
● No special certifications required for operators of steam absorption chiller
Equipment Information
BROAD Absorption Chiller
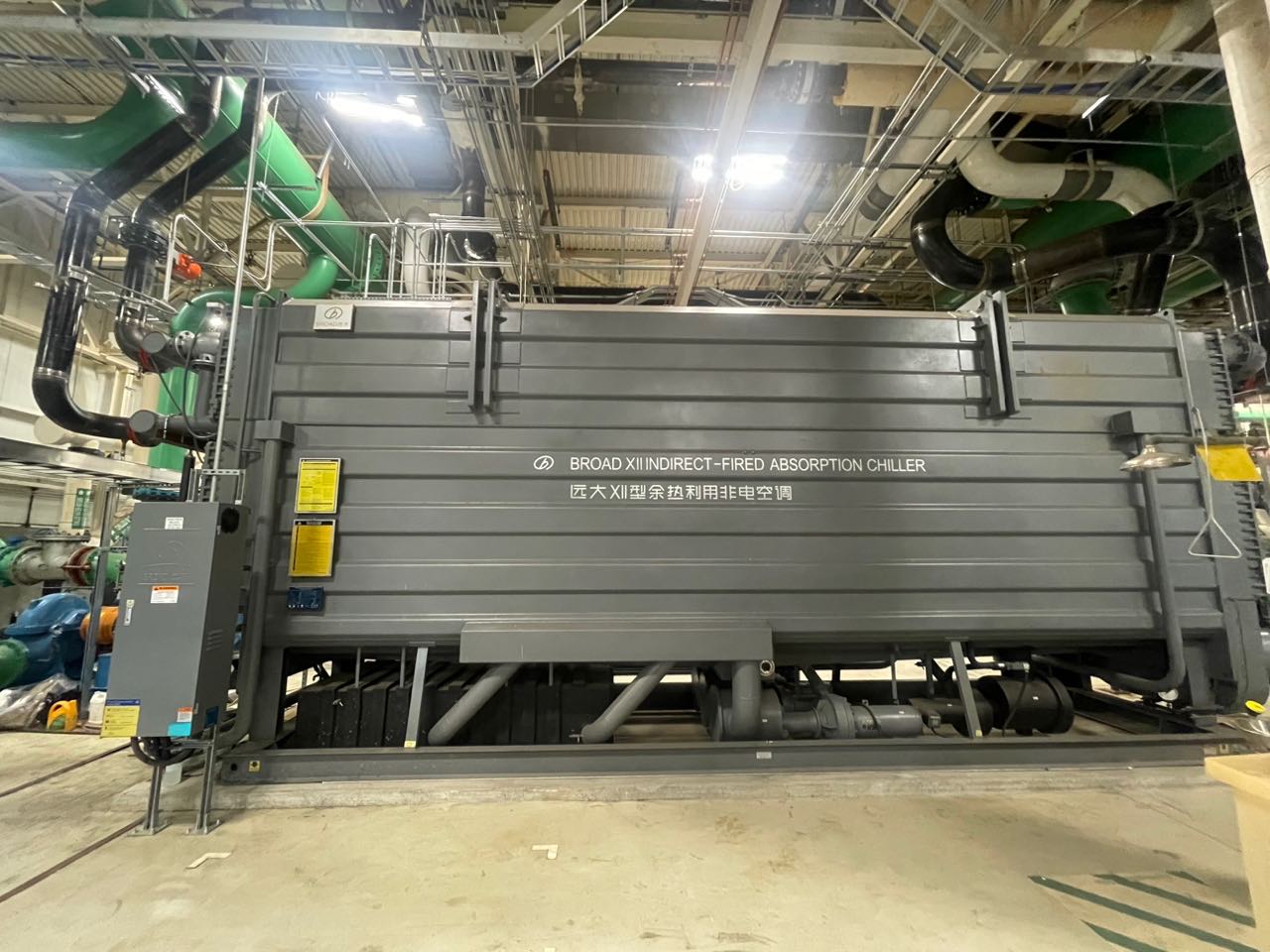
Model: Single Stage Hot Water Absorption Chiller BDH500
Cooling Capacity: 1617RT
Heat Source: Hot water from turbine exhaust recovery boiler
Project Gallery
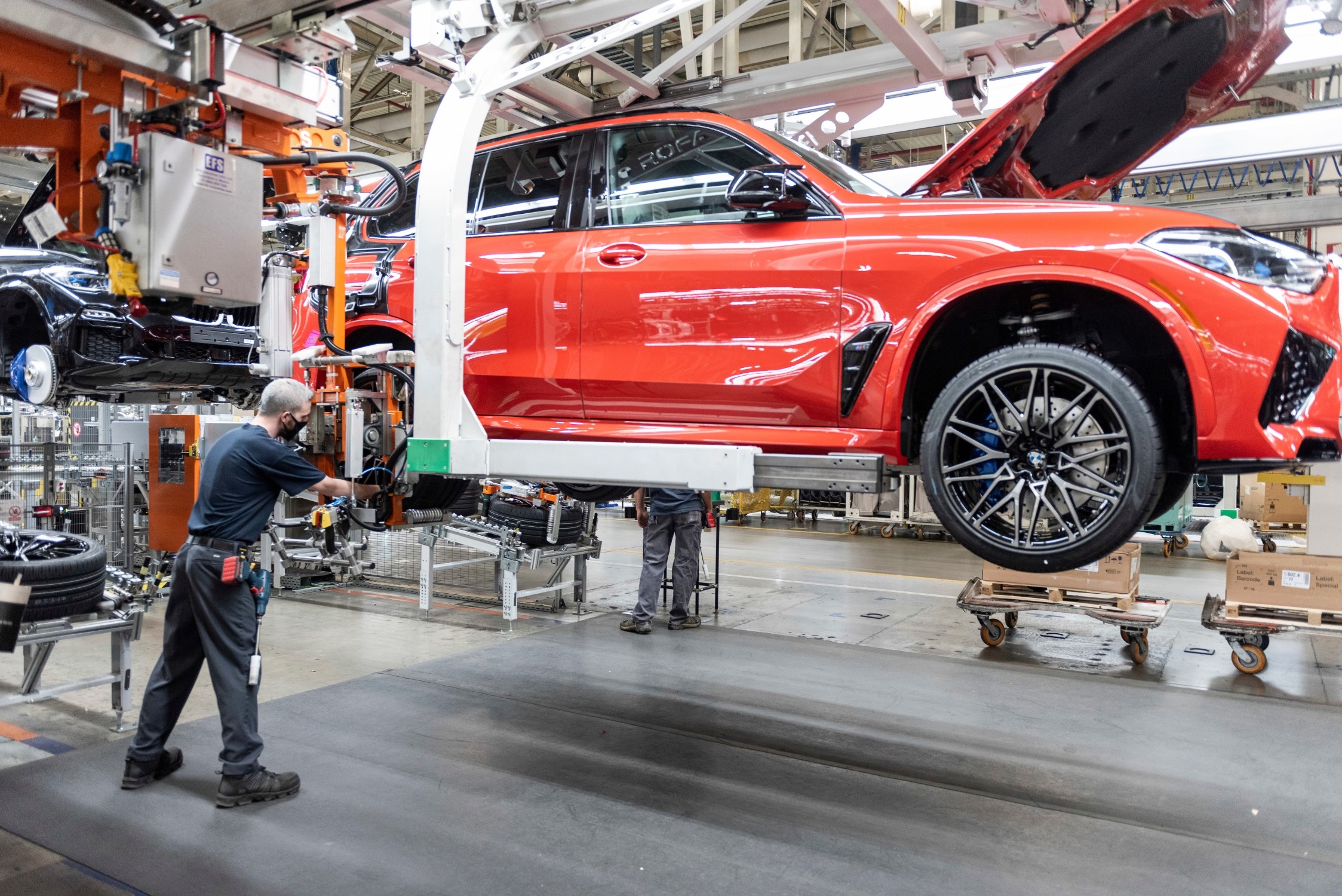
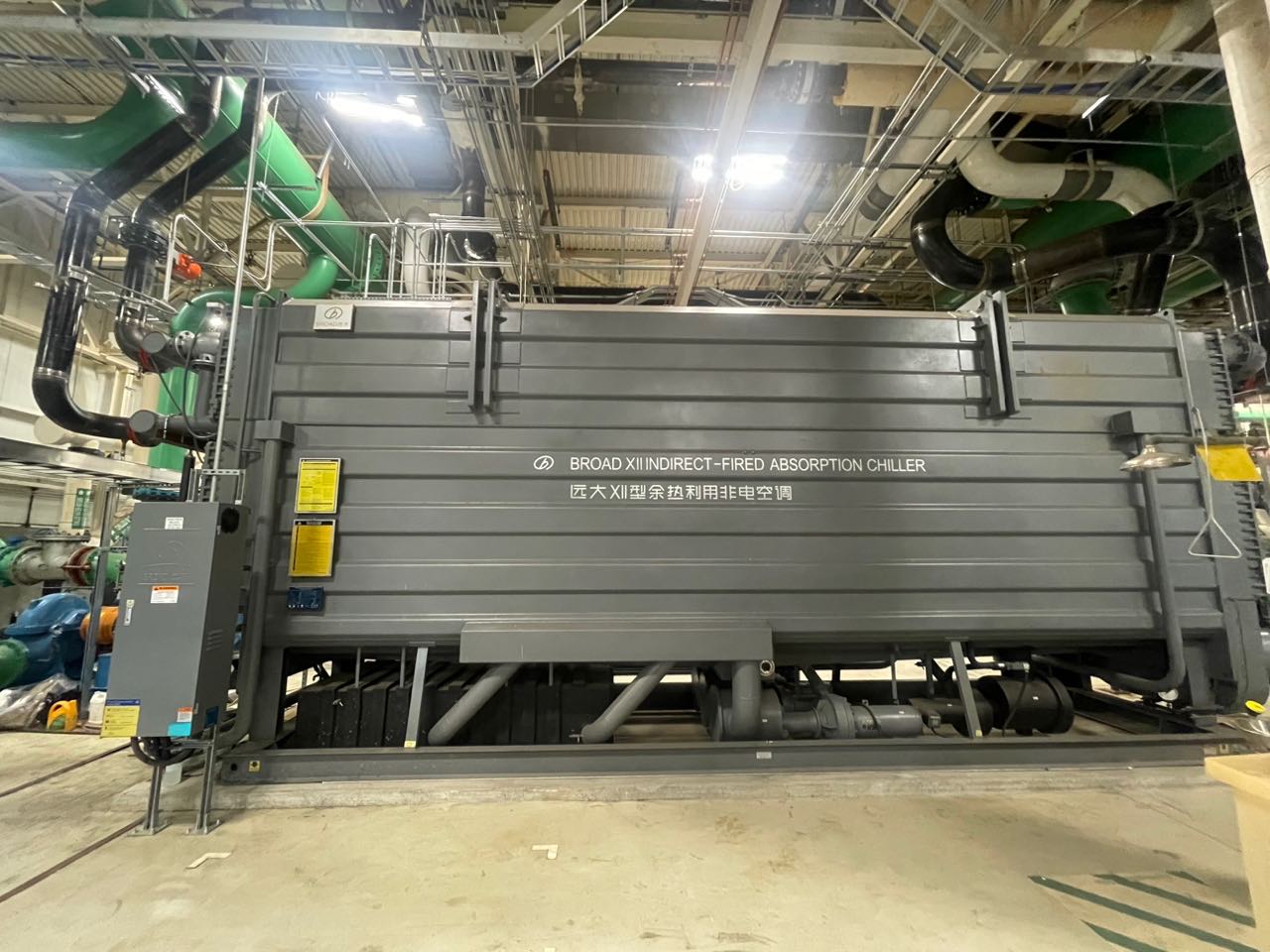
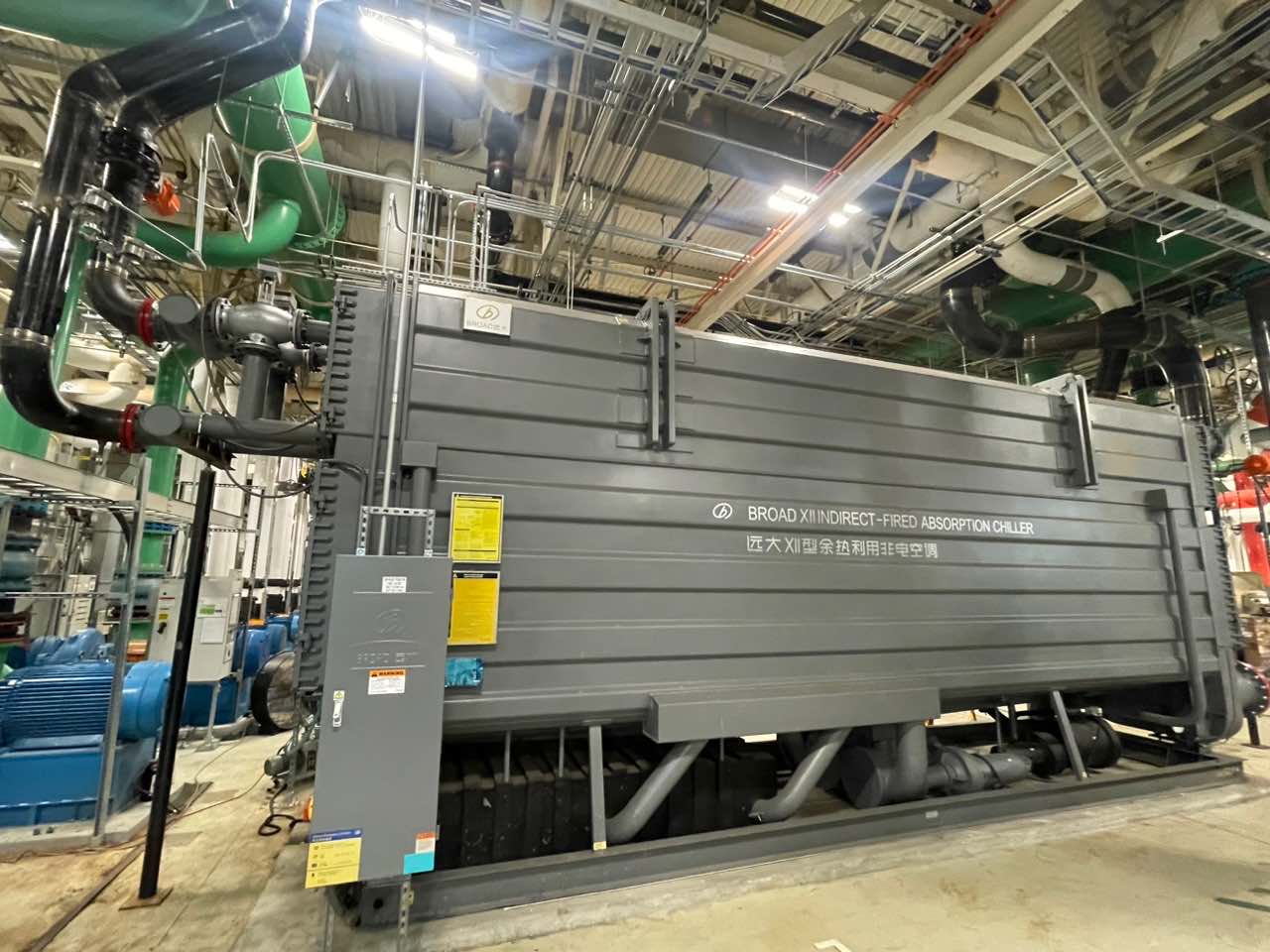